Press Brake Tools Types
The standard press brake tools Types
Press Brake Tooling is classified into press brake punches and bottom dies. They work by folding your workpiece between a matched bending punch and die, to bend the material into pre-determined shapes. The Press brake punch and dies have a segmented and standard length. The V-dies are the most common tool punch types for the bending process. The bottom dies for die openings can handle a variety of materials and bend angles. below are the most common press brake tools types that we often use for sheet metal working bends.
90 degree dies
The tool punch types are widely used for bottoming operations. The die opening dimension depends on the bending machine punch and die material thickness.
Rolla V bending dies
Rolla V Dies have a cylindrical shape with an 88-degree V-notch cut. The die is an anvil over which the rocker bends the sheet.
Acute angle dies for air-bending
They can be used to produce acute, 90-degree bending angles by matched bending punch and die.
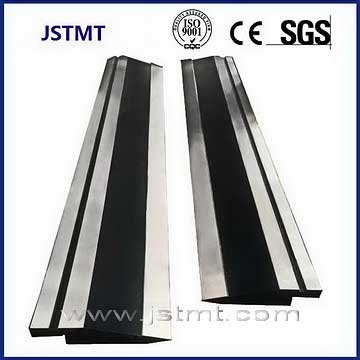
Gooseneck dies for return-flanging
The press brake punch tool is designed to allow for the clearance of already-formed flanges.
Offset dies
a combination punch and die set that bends two angles in one stroke to produce a Z shape.
Hemming dies.
Two-stage dies combine an acute angle die with a flattening tool.
Stamping dies
There are many ways to build dies to produce seams in sheets and tubes.
Radius dies
A radiused bend can be produced by a rounded punch. The bottom die may be a V-die or may include a spring pad or rubber pad to form the bottom of the die.
Beading dies
A bead or a “stopped rib” may be a feature that stiffens the resulting part. The punch has a rounded head with flat shoulders on each side of the bead. The bottom die is the inverse of the punch.
Curling dies
The die forms a curled or coiled edge on the sheet.
Tube- and pipe-forming dies
a first operation bends the edges of the sheet to make the piece roll-up. Then a die similar to a curling die causes the tube to be formed. Larger tubes are formed over a mandrel.
Four-way die blocks
A single die block may have a V machined into each of four sides for ease of changeover of small jobs.
Channel-forming dies
A press brake punch tool can be pressed into a die to form two angles at the bottom of the sheet, forming an annular channel.
U-bending dies
Similar to channel forming, but with a rounded bottom. Spring back may be a problem and a means may need to be provided for countering it.
Box-forming dies
While a box may be formed by simple angle bends on each side, the different side lengths of a rectangular box must be accommodated by building the punch in sections. The punch also needs to be high enough to accommodate the height of the resulting box’s sides.
Corrugating dies
Such dies have a wavy surface and may involve spring-loaded punch elements.
Multiple-bend dies
A die set may be built in the shape of the desired profile and form several bends on a single stroke of the press.
Rocker-type dies
A rocker insert in the punch may allow for some side-to-side motion, in addition to the up-and-down motion of the press.
Press Brake Tools types selections
The Tooling Systems include American Style Tooling, European Style Tooling, and WILA/New Standard Tooling.
Understanding these different types is crucial for selecting the correct tooling for a specific bending application,The press brake tools types selection depends on material type, thickness, and desired bend geometry:
Material Thickness: Thicker materials require larger V-die openings and more robust punches.
Bend Radius: The desired radius of the bend determines the punch and die selection.
Material Type: Softer materials like aluminum may require different tooling than harder materials like stainless steel.
Bend Angle: Acute, obtuse, or 90° bends require specific tooling shapes.
Production Volume: High-volume production may benefit from specialized or automated tooling for efficiency.
Tool Material: Tooling is often made from high-carbon steel, alloy steel, or tool steel for durability. Coatings may be used for enhanced wear resistance.
Press Brake Tools types are used depending on the material, production requirements, and machine compatibility, Proper selection and maintenance of tooling are essential for achieving high-quality bends and maximizing productivity. If you are not sure what types of press brake tools to choose, please contact for custom press brake tools.
Leave a Reply