How to Choose Press Brake Crowning System
Press Brake is an important bending tool for sheet metal plates, the precision of the bending process directly decides the accuracy of sheet bends.
What is crowning in Bending?
when a heavy machine applies bending force on the sheet metal to form shapes, There is a reaction (opposite) force from the sheet that reflects on the machine. This results in an inconsistent bending angle deflection across the full length of the machine. It can lead to a bowed appearance in the part or “the canoe effect” due to machine deflection. To improve the bending accuracy, the press brake crowning system can help to solve it. this crowning includes mechanical compensation and hydraulic compensation.
When we choose a CNC sheet bender, Not only tonnage capacity, throat depth, and column spacing, but also the crowning types also need to be considered. As the crowning systems have different requires to press brake operators & working precision. So It is very important for buyers to know which press brake crowning system to choose.
Press Brake Hydraulic Crowning vs Mechanical Crowning
What is a Hydraulic Press brake crowning system? The small cylinders are under the worktable. when machine ram and bed got deforms, additional force is applied through small cylinders and ready to compensate it. so It can reduce the influence of Ram or Die deformation on the folded plate.
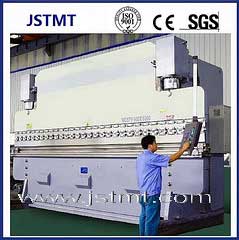
Working principle of Hydraulic Press brake crowning system
The hydraulic crowning system uses small cylinders to compensate for the worktable. Setting bending parameters in programming software based on the plate length and thickness. the crowning amount can be auto-calculated and transmitted to the compensation amplifier. The hydraulic proportional valve gets this signal, and controls the small cylinder to bulge and reduce the deflection.
Hydraulic press brake crowning will be affected by many factors. Oil leaking & pipe loosen will affect the amount, which leads to the difference of each plating process.
The advantage of Hydraulic press brake crowning is:
- Easy and simple to operate with consistent bends.
- It requires less technical for the press brake operators with high precision.
- Make sure full contact between the upper die and the sheet, and avoid displacement of the sheet metal.
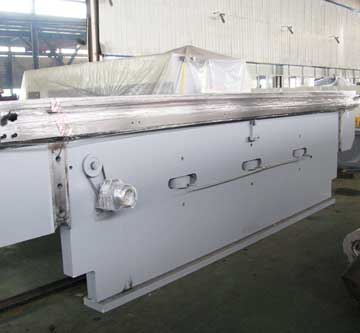
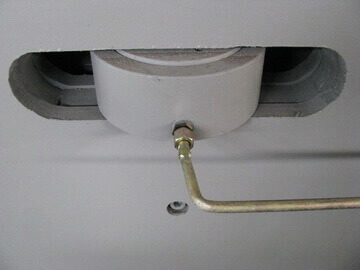
Working principle of Mechanical compensation
- Mechanical crowning systems are installed in place of a bottom tool holder. They typically feature either mechanical or hydraulic clamping as options. They also typically feature different drive designs, from analog to digital readouts and from hand crank assemblies to CNC motors.
- The mechanical press brake crowning system uses wedge blocks to compensate for the worktable. The oblique wedge block has multiple groups of blocks for mass production. the mechanical crowning is simple without any leakage. However, mechanical compensation is easy broken parts that affect the effects.
- Mechanical crowning operation requires higher requirements for multi-bends. If the same workpiece needs multiple bends, workers need to make a localized adjustment in real-time.
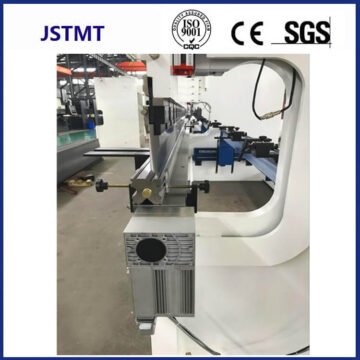
Leave a Reply