JSTMT produces sheet metal cutting & bending Machine products, including Hydraulic & CNC Press Brake, Shearing Machine, Press Brake dies, Lathe, Ironworker, and Press Machine. It is used in sheet metal plate manufacturing, cutting, bending, stamping, and forming production lines. The sheet metal machines can provide a one-stop solution for our common & complex metal parts. and It can improve the precision of the sheet metal machines with desired shapes.
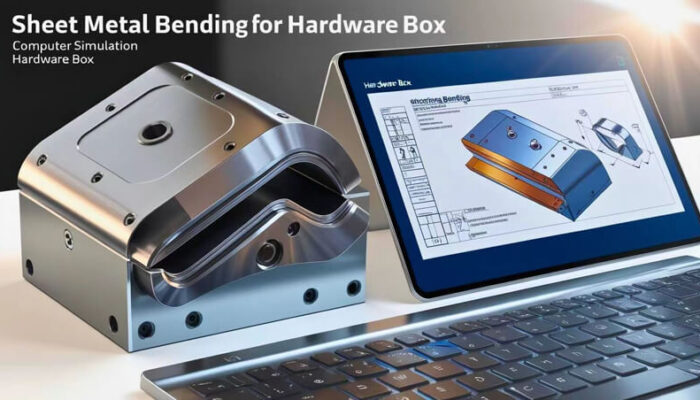